The Advanced Light Helicopter (ALH) Dhruv was once a major success story for Hindustan Aeronautics Limited (HAL). However, recent events highlight significant concerns regarding its manufacturing quality. With over 23 crashes leading to the loss of several pilots, the Indian defense establishment must prioritize fixing these issues. Addressing the safety and reliability of ALH Dhruv is crucial for India’s defense capabilities.
Grounded ALH Fleet: Cost and Capability Concerns
The grounding of ALH Dhruv is a serious issue from both cost and capability perspectives. The recent crash, attributed to a cracked swash plate, raises multiple concerns. Cracks in such a critical structural component suggest deeper problems. These include flaws in manufacturing quality, preventive maintenance lapses, deficiencies in health monitoring systems, and shortcomings in upkeep protocols. Each of these factors must be investigated thoroughly.
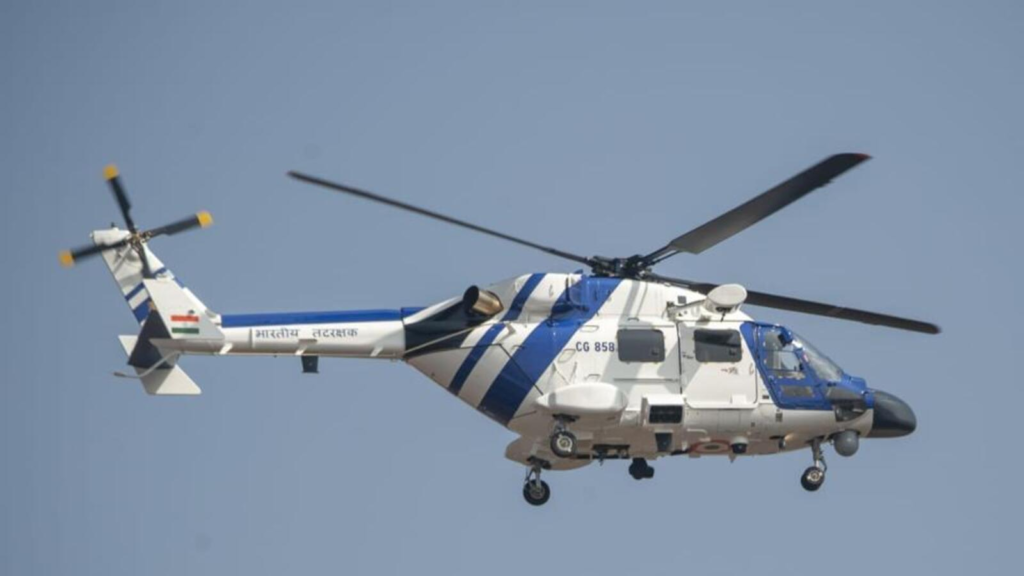
Identifying and Rectifying Issues in ALH
A comprehensive analysis of ALH Dhruv is necessary to identify and fix all existing problems. However, predicting every possible failure is impossible. For instance, when HAL and CEMILAC worked on control rod issues a year ago, they could not have anticipated the swash plate cracking soon after. Ideally, every component should undergo a strict quality assurance process. Yet, incidents like these raise concerns about HAL’s entire quality assurance protocol.
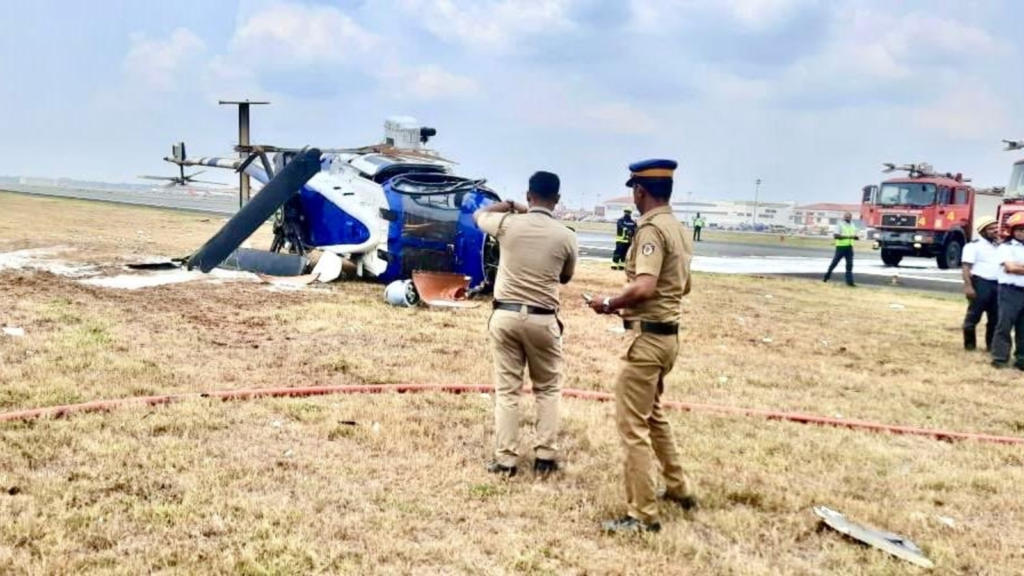
Overhauling Quality Assurance and Accountability
To prevent future failures, HAL must revamp its quality assurance system and enforce accountability. The safety of pilots is paramount, and any negligence cannot be ignored. Ensuring that every component meets the highest safety standards is critical. Without accountability, the lives of those operating these machines remain at risk.
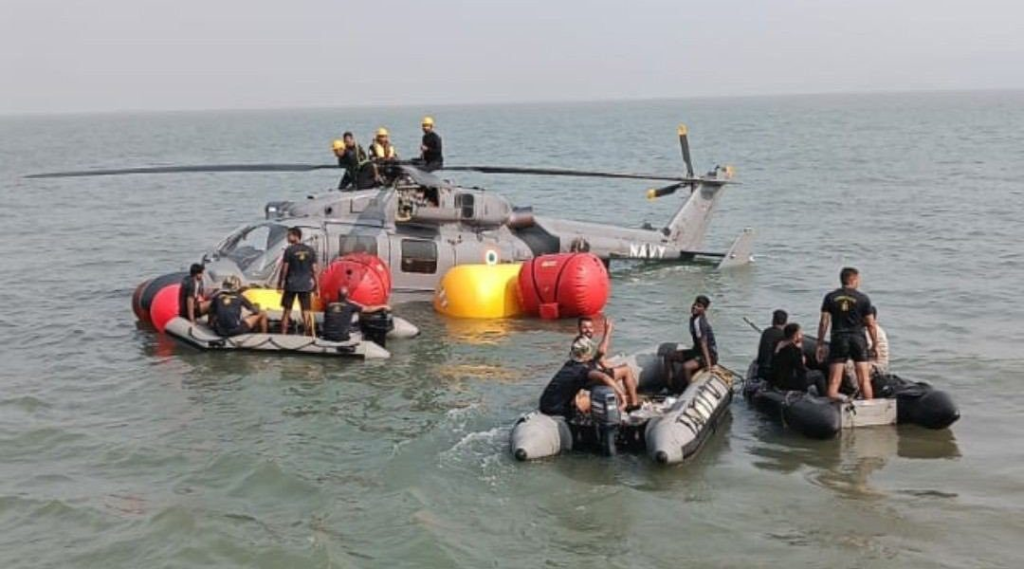
Historical References
Recent discussions have included the use of old photographs from 2007-08 to criticize ALH Dhruv. While frustration regarding the helicopter’s reliability is understandable, misrepresenting past issues does not contribute to a constructive dialogue. Instead, past challenges should be analyzed to compare HAL’s response then versus now. While the specific problems may differ, the approach toward rectification remains a key concern.
Advanced Technology, Yet Quality Concerns Persist
ALH Dhruv was developed at a time when India had no prior experience in helicopter manufacturing. Despite this, HAL aimed high and incorporated cutting-edge technologies, including:
- Resin Transfer Molding (RTM) and Autoclave Curing for carbon-fiber reinforced polymer (CFRP) and glass-fiber composite fuselage, in contrast to metallic monocoque designs like the H125.
- Resin Film Infusion (RFI) in Vacuum-Assisted Molding to achieve near-net shape fabrication for the BERP-inspired 4-blade composite rotor, unlike the hand-laminated prepreg composite blade construction of the H125.
- Friction Stir Welding (FSW) for aluminum-lithium fuselage joints, as opposed to traditional TIG/MIG welding and cold expansion hole processing used in H125.
- Resin Infusion Molding (RIM) and Filament Winding Technology (FWT) for tail boom fabrication, unlike the riveted and bonded monolithic structures of H125.
- 5-axis CNC machining centers with adaptive process control and laser-based automated drilling systems.
- Plasma Electrolytic Oxidation (PEO) for aluminum protection, whereas H125 helicopters rely on chromate-based anodizing and epoxy primers.
ALH Dhruv integrates state-of-the-art materials and manufacturing techniques. However, the lack of stringent quality assurance can undermine the hard work of designers, manufacturers, and military personnel who provide crucial feedback and operational insights.
The ALH Dhruv represents India’s ambition in indigenous helicopter manufacturing. However, frequent crashes and maintenance issues highlight critical flaws in HAL’s production and quality control. The Indian defense establishment must ensure a complete overhaul of the quality assurance process. Only then can ALH Dhruv fulfill its intended role as a reliable and effective platform for the armed forces. Ensuring accountability and rectifying these flaws is not just about improving a machine—it is about protecting the lives of those who operate it.
no matter how much advance manufacturing technology you use if the raw material used to make these have low quality then it us bound to fail in the long run. Due to tight budget there is has always been a pressure on HAL(other DPSU’s also suffer) to make products at lower cost which may have forced them to do cost cutting with materials which they didn’t think would cause significant problem in the long run but now it is proving to be fatal. this also raises concerns on safety and certification board if there is major problem then gow did it get its air worthy/millitary worthy certification in the testing
I feel so disheartened. This is success story going bad.
how can anyone expect to get the politics of the country engaged in the filling the government services with local mafia who support to win the election since the indipendence
However hard one may try, but you can’t hide the fact that the Emperor (ALH) has no clothes. A disinterested aircraft manufacturing PSU, ‘hands-off’ mentality quality assurance agencies and timid Service Headquarters (and their army of HAL co-located Service Project Offices), have all contributed to this terrible mess that was to be the showpiece of Indian aviation technology prowess. The stigma which gave our defence exports a bad name for a decade (2012-2022) was due to the HAL-ALH export to Ecuador fiasco wherein within a period of five years, nearly 50 percent ALH helicopters had crashed there, leading to the infamous unilateral cancellation of the deal by Ecuador government. Whilst the design is brilliant, considering that it was the first time such a complex machine was being attempted by the novice Indian design agencies, the entire good work was brought to nought by the shoddy execution and pathetic manufacturing processes of HAL. Even now after so many accidents, HAL refuses to learn the real lessons of aircraft manufacturing processes that are steeped in absolute integrity and uncompromising quality control. Instead, the glaring defects are back pedalled in the midst of self-glorification of ‘Indeginisation’ and ‘Atmanirbharta’. However laudable this swadeshi effort may be, but it is to be remembered that HAL is no simplified ‘Charkha’ that will produce a ‘Khadi’ helicopter unless the basic dictums of correct and highest quality aircraft manufacturing standards are not ingrained in the ranks and file of HAL.
India should have involved top Engineering heavyweights like L&T in critical defense manufacturing ! It would have been a differnt situation today !
ALH Dhruv or any defence-related abnormal failures definitely show the intrusion of foreign hands in multiple ways in our government-owned defence industry. The government has consistently failed to control foreign interference in our defence industry.
Indian defence industry continual under control of such people who are not answerable nor accountable over delays or output or failures in that industry. The government is spending huge money over these units without any desired outcome. DRDO or HAL are just white elephants and eating up taxpayers money without any accountability.
HAL need to establish reliability lab where critical components needs to be tested for number of cycles. This will address the unexpected failures/issues.
I think the writer does not know the technologies exactly used in ALH..There is no resin trasfer moulding , resin infusion etc are used.Well proven composite manufacturing technology is used for the structure and rotor blades. Extensive testing of each component was done specifically for rotor systems including blades. Failures may happen during usage depending on forces applied during flights as well poor maintenance. Can anyone audit the way users use the Helicopters, maintain and carry out repair. whether the users use lifed materials like seals, lifed resins, etc. If one compares with other helicopters, one can find that failures do occur. but foreign companies know how to manage media and the users. If someone remember Bell helicopter was involved in an accident in which one Andra Chief minister was died but no Bell helicopter was grounded. Similarly two aircraft of Boeing met with accidents and hundreds of travellers were died but Boeing managed the situation and again all the aircraft are flying without any changes. HAL should handle the situation professionally taking help of experts in manufacturing and carring out process audit of major components. As I know there is not shortcomings in design of ALH. Problem may be in maintenance and servicing as guessed by HAL Chairman. HAL and users should also carryout the audit of maintenance processes including lives of raw materials used by users and strengthen the quality systems during manufacturing, testing and maintenance. I am confident that HAL will come out from this situation in flying colour. Jai Hind.
The problem facing the HAL is known for long Time. The quality man cannot be responsible directly to the boss who is also accountable to meet annual production tasks. But the quality hierarchy is very much diluted at HAL and it is only in paper that quality is a priority..
The problem facing the HAL is known for long Time. The quality man cannot be responsible directly to the boss who is also accountable to meet annual production tasks. But the quality hierarchy is very much diluted at HAL and it is only in paper that quality is a priority..
well said sir.
End of ALH dhruv project and probably LCH,LUH as well.
LCA is heading towards the same.
back 2022 when I pointed out issues with LUH including tail rotor, alpha defense trolled me. hope engineer kid of alpha defense has grown up by now and smelling reality of HAL.
I organized Guest Lecture for RWRDC on 27 Niov 2027 as part of HAL Quality Month Celebrations on “Cost of Quality’. in my Lecture, I tried to bring clarity to the importance Design for Six Sigma (DFSS) in the process of TQM of ALH project & identify this as a problem thru’ Failure Modes & EffectsAnalysis . If this is to be strictly followed across the organization, this PSU needn’t fall to the onslaught of disinvestment & fill pockets of private investors.
MSR Sathyanarayana, NIQR +91 9886304082
Friends, plz read 27 Npv 2027 in my earlier comment as 27 Nov 2021
I was strongly advocating to clear army and airforce skid version ALH to clear for flight as these are 4.5ton class helicopters experiencing loads less than 5.5ton coastguard and naval helicopters.Thank GOD it happened at the end .