The Indian Army and Air Force will now resume ALH Dhruv operations. The Defect Investigation Committee reviewed all safety concerns. Based on its recommendations, officials cleared the helicopters for flight. Engineers and users jointly prepared a time-bound plan. Revised protocols will guide maintenance during the resumption phase. This ensures operational safety and service continuity.
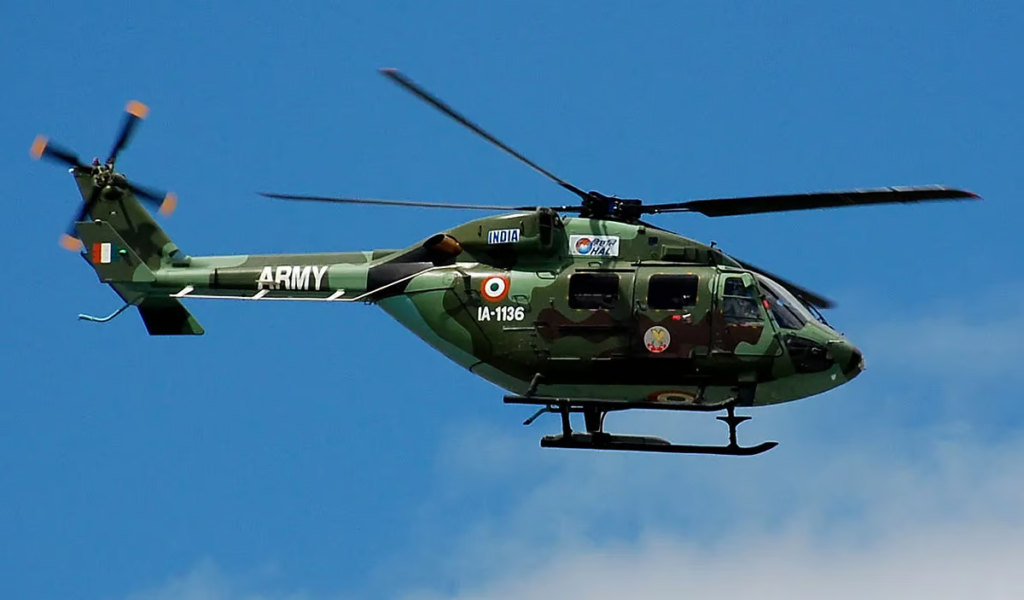
ALH Dhruv: Swash Plate Crack Investigation Provides Key Insight
Investigators flagged a swash plate crack as the main defect in ALH helicopters. However, helicopters equipped with skis showed no cracks. These ski-equipped units operated safely during the entire inspection process. Clearly, helicopter configuration affects component fatigue. This key finding supports tailored maintenance for different ALH Dhruv variants.
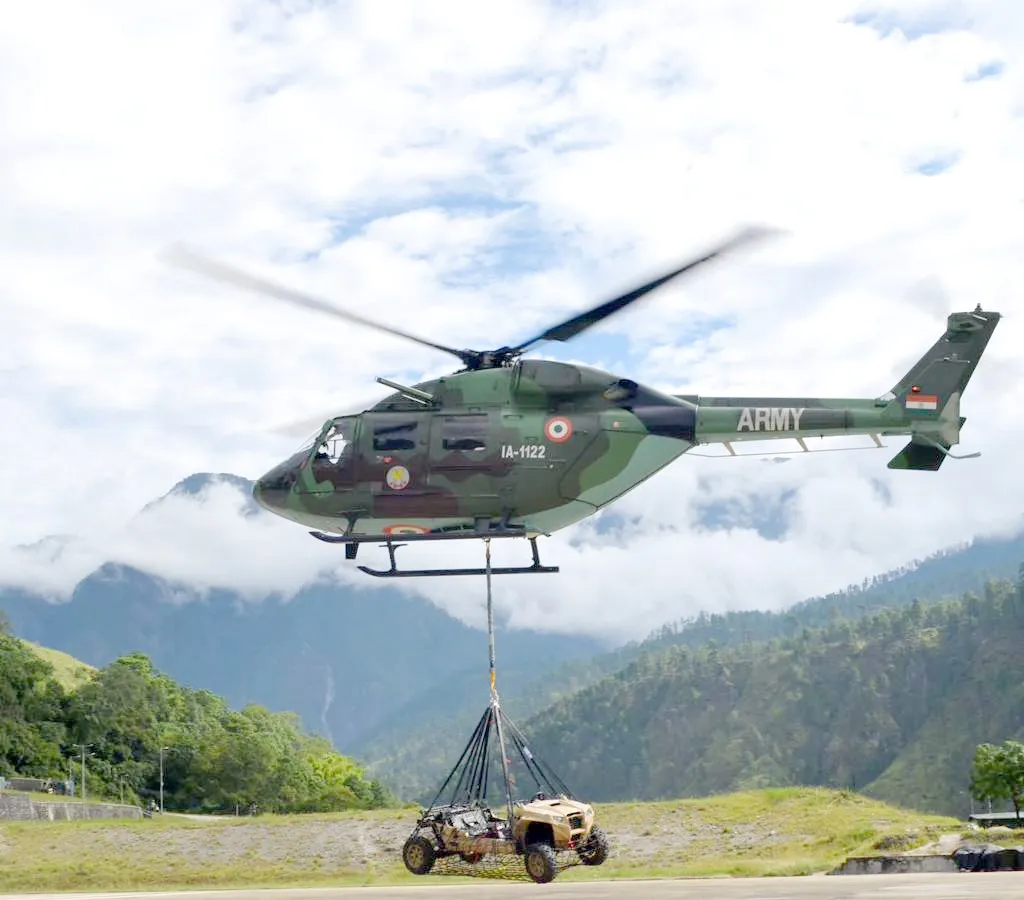
ALH Mk-III (IN/CG): High Operational Load Drives Fatigue
The Indian Navy and Coast Guard fly the ALH Mk-III at heavier all-up weights. Consequently, these helicopters experience higher mechanical stress. Frequent taxiing on ground also adds to dynamic loading. Technicians found flawed taxiing methods worsening component fatigue. Among two taxiing techniques, only one proves safer long term.
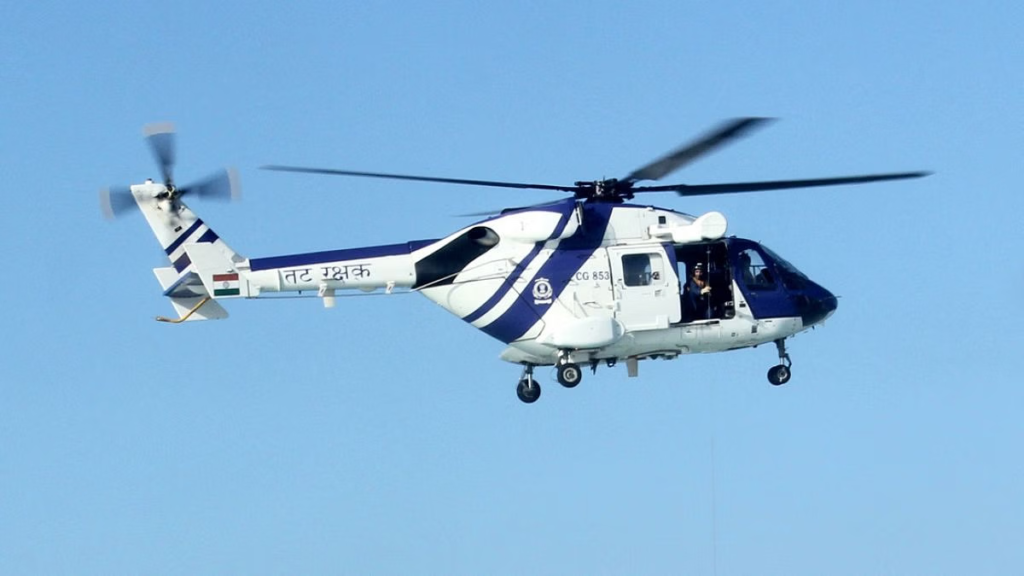
Taxiing Technique Impacts Structural Health
The first method uses aggressive cyclic with almost no collective. This causes high dynamic loads on key assemblies. Apache helicopters suffered early rotor hub failures using similar flawed techniques. In contrast, the second method applies light collective and smooth cyclic. This approach reduces fatigue and supports longer component life. Manuals should now guide pilots toward correct taxiing.
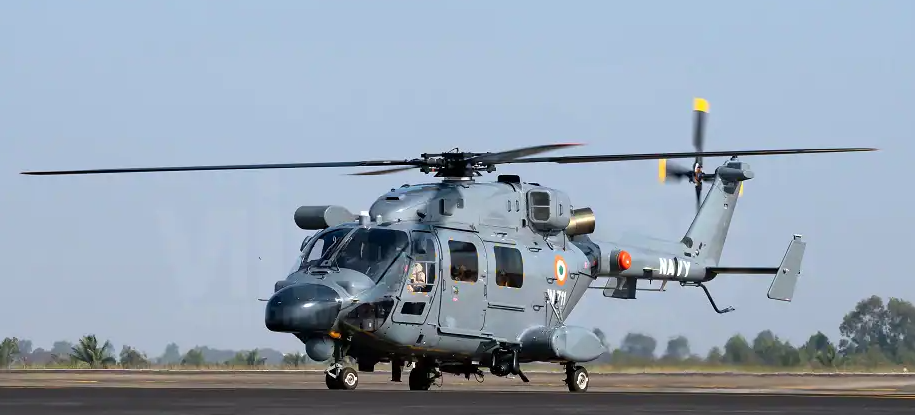
Greater Strain from Ship-Based Operations
Ship deck landings increase structural loads on the ALH. Smaller naval vessels pitch and roll during operations. This motion creates extra stress during take-offs and landings. In addition, the ship’s wake increases gust loads on rotors. These dynamic loads severely impact the landing gear and airframe. Naval helicopters thus face unique fatigue challenges.
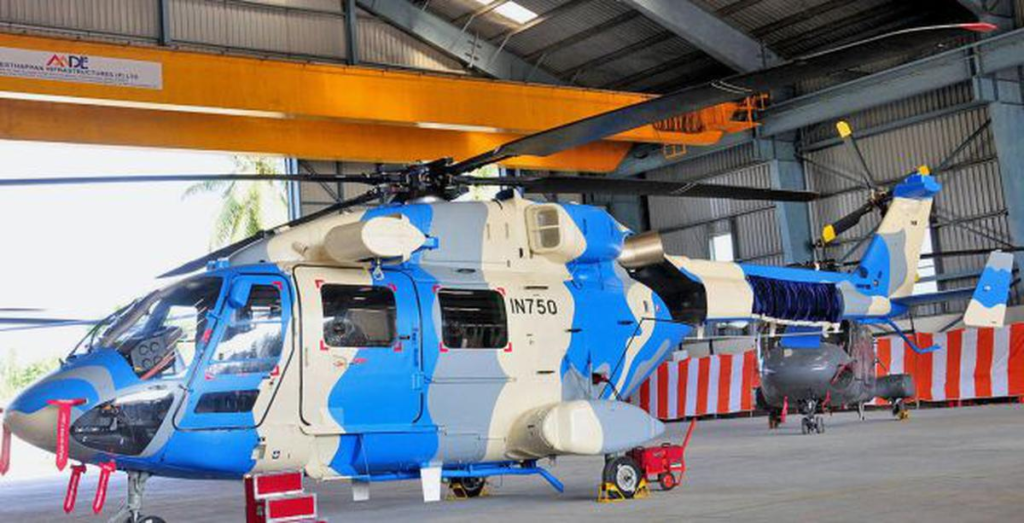
ALH Dhruv Fatigue Life Requires Scientific Reassessment
Fatigue life prediction remains inconsistent across global helicopter models. A 1980 study revealed vast estimation gaps. The same pitch link showed fatigue lives from 9 to 27,816 hours. These differences reflect varying methods among OEMs. Therefore, HAL must use real-time Flight Data Recorder (FDR) inputs. Engineers must model fatigue using actual Dhruv flight profiles.
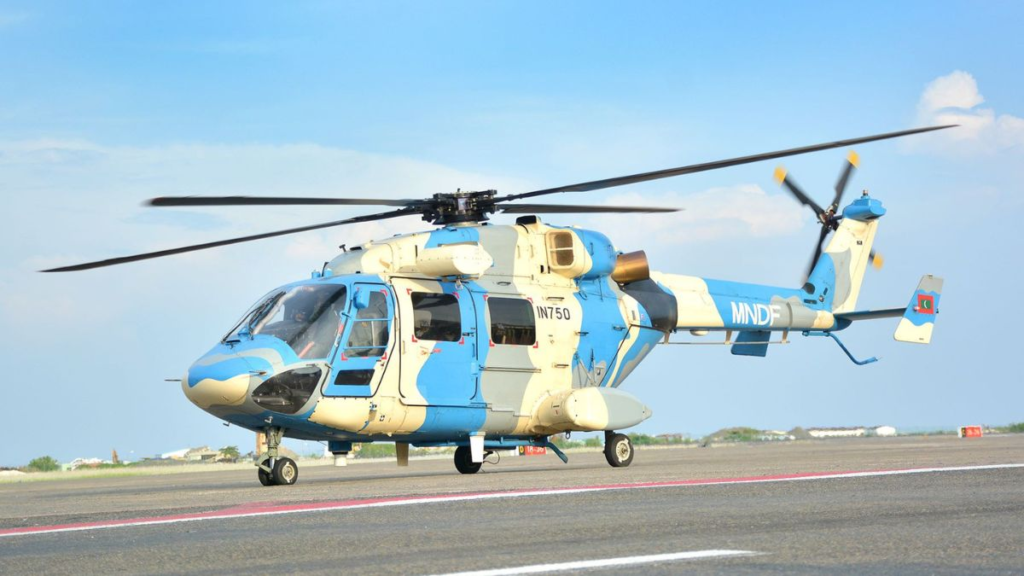
HAL Must Recalculate ALH Dhruv Component Fatigue
HAL must urgently reassess swash plate fatigue on ALH helicopters. This process should include new simulations and real-world flight data. Engineers may need to revise fatigue life of other components too. Data links swash plate failure to high taxiing and rough ship landings. Using correct techniques will limit these damaging loads.
Solutions for Enhancing ALH Dhruv Safety and Reliability
HAL should update the ALH Dhruv flight manual without delay. New guidelines must promote correct taxiing procedures. Commanders must limit high-stress actions during daily operations. If needed, inspections should occur more often. Operators may also replace critical parts earlier. These changes will enhance safety and extend the service life of ALH helicopters.
Have a heart, Alphadefense!
Thanks for this deep information. Really brilliant. This sort of information is not easily available out there.
the helicopter has a system for health and usage monitoring HUMS. it should have continuous monitoring of the health of most of the critical components including sauce plate. I hope it has been monitord in the last 25 years and it should be monitor me the next 25 years of life. if it is not, action should be taken immediately to include the Swash plate parameters are any other critical structure and component into the harms software with immediate effect. they should keep they services in greater peace
the helicopter has a system for health and usage monitoring HUMS. it should have continuous monitoring of the health of most of the critical components including swash plate. I hope it has been monitord in the last 25 years and it should be monitored for the next 25 years of life. if it is not, action should be taken immediately to include the Swash plate parameters or any other critical structure and component into the HUMS software with immediate effect. they should keep they services in greater peace