– Praful Kumar
DRDO’s Armament Research and Development Establishment Partners with Stumpp Schuele & Somappa Defence (SSS Defence) for CERAKOTE Coating Technology Development
The Armament Research and Development Establishment (ARDE), part of India’s Defense Research and Development Organization (DRDO), has officially partnered with SSS Defence to advance the development and application of CERAKOTE coating technology for small arms. This collaboration aims to enhance the durability and performance of critical firearm components such as barrels, bolts, and receivers. ARDE’s long-term vision is to expand CERAKOTE’s usage to larger components and systems, based on successful testing and evaluation.
As part of the agreement, SSS Defence, a leading Indian defense company and certified CERAKOTE applicator, will design and establish a processing facility for this purpose. The facility may be either semi-automatic or fully automatic, depending on operational requirements. The project’s scope includes the delivery of 200 units of ceramic-coated components—supplied by ARDE—for rigorous testing and evaluation.
What is CERAKOTE?
CERAKOTE is a ceramic-based firearm coating known for its exceptional durability, corrosion resistance, and wear resistance. It provides a high level of protection against scratches, abrasion, and chemicals, making it ideal for use on firearms. In addition to performance benefits, CERAKOTE offers customization options through a variety of colors and finishes, allowing for both aesthetic and functional enhancements.
Key CERAKOTE Specifications for ARDE-SSS Defence Project
- Hardness: The coating must have a hardness level between 8-10 on Moh’s scale. Components will be tested according to the ASTM D3363 standard.
- Mohs Scale : The Mohs Scale is a qualitative scale used to measure the hardness of materials based on their ability to scratch softer substances. It ranges from 1 to 10, with 1 being the softest (like talc) and 10 being the hardest (like diamond). The scale helps determine how resistant a material is to scratches and wear. The CERAKOTE coating is expected to have a hardness between 8-10 on Mohs scale, meaning it is quite hard and resistant to abrasion, with 8 corresponding to materials like topaz and 10 to diamond.
- ASTM D3363 Standard : The ASTM D3363 standard is a method used to determine the hardness of coatings by using pencil hardness testing. This test involves pressing pencils with leads of varying hardness (graded from soft to hard) against the coated surface to evaluate its resistance to indentation or scratching. The goal is to find the hardest pencil that can be used without damaging the coating, which provides a consistent measurement of the coating’s hardness.
- Thermal Properties: The coating is designed to withstand temperatures up to 600°C. After exposure, components will undergo visual inspections to assess any damage.
- Corrosion Resistance: Coated components must pass a 1000-hour salt bath test, ensuring high corrosion resistance. Testing will follow the ASTM B117 standard.
- Thickness: The CERAKOTE coating will have a thickness between 10-25 µm, with two components tested using both destructive and non-destructive methods.
- Adhesion Properties: The coating should exhibit excellent adhesion, with a 5B rating. Adhesion tests will be conducted on two components using the ASTM D3359 standard.
- Visual Inspection: Each CERAKOTE-coated component will undergo a visual inspection to confirm that the surface is lustrous and free from pits, blisters, exfoliation, or uncoated areas. NABL-certified labs will provide test certificates, though ARDE reserves the right to conduct further testing.
Stealth Aspect of CERAKOTE
Reflection and Stealth: CERAKOTE can be applied in matte finishes that reduce surface reflection. This is crucial for military and tactical operations, where reflections can expose a shooter or equipment under night vision devices (NVDs). A non-reflective coating helps maintain stealth by minimizing the chance of detection under infrared (IR) light used by night vision systems.
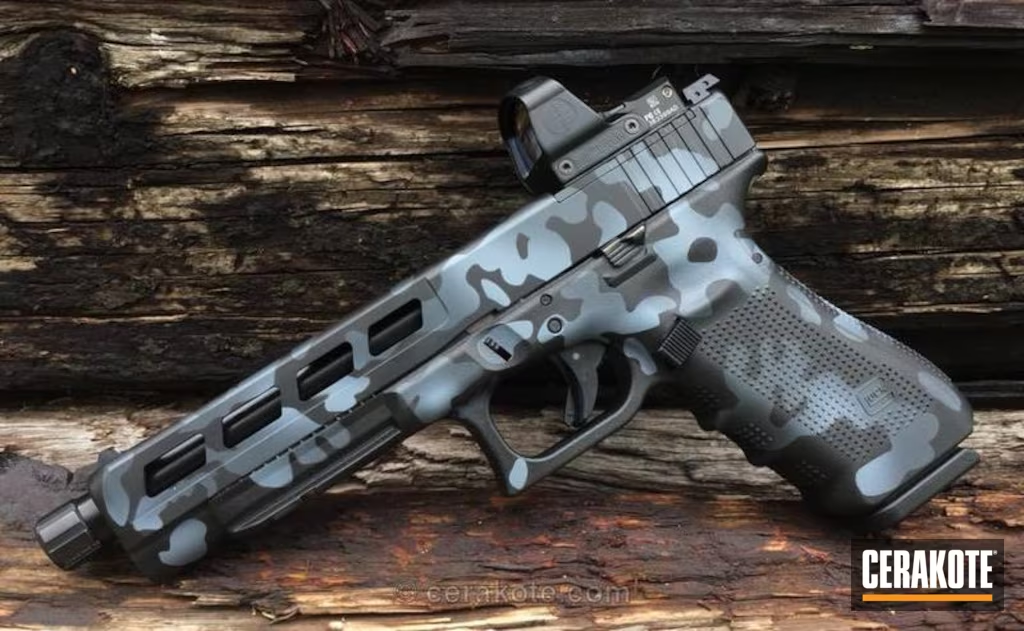
Infrared Signature Management: Some CERAKOTE coatings are designed to have infrared-reflective properties, meaning they reflect less IR light, which can help reduce the heat signature of the coated object. This makes it harder for the object to be detected by night vision devices or thermal imaging systems, enhancing camouflage in low-light environments.
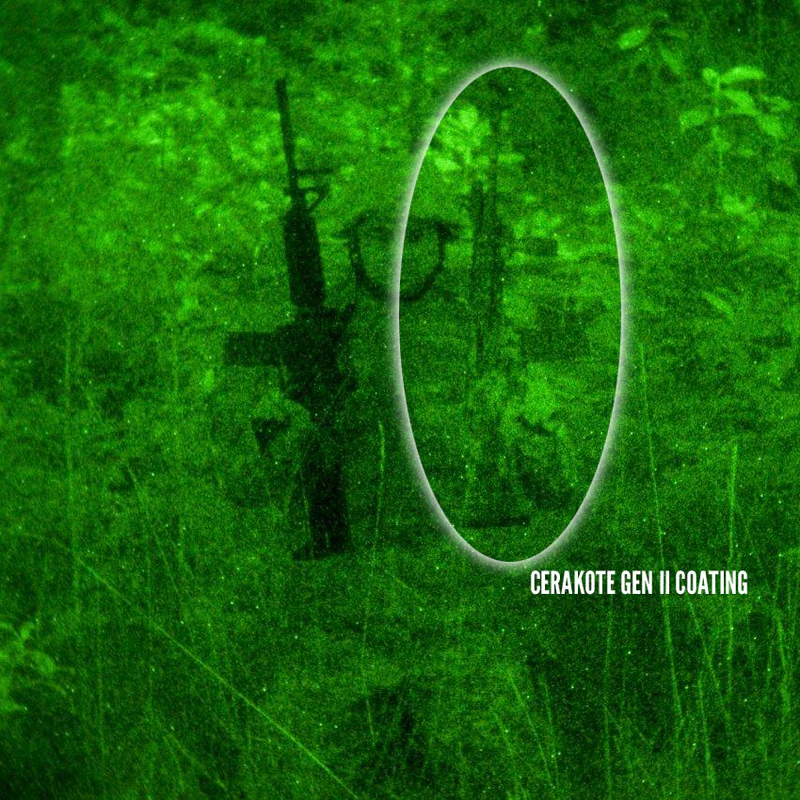
Customization for Environment: CERAKOTE offers a wide range of colors and finishes that can be customized for specific environments. For example, darker, non-reflective coatings can blend better into night-time landscapes, which is beneficial for operations conducted using night vision, ensuring the equipment does not stand out under NVDs.
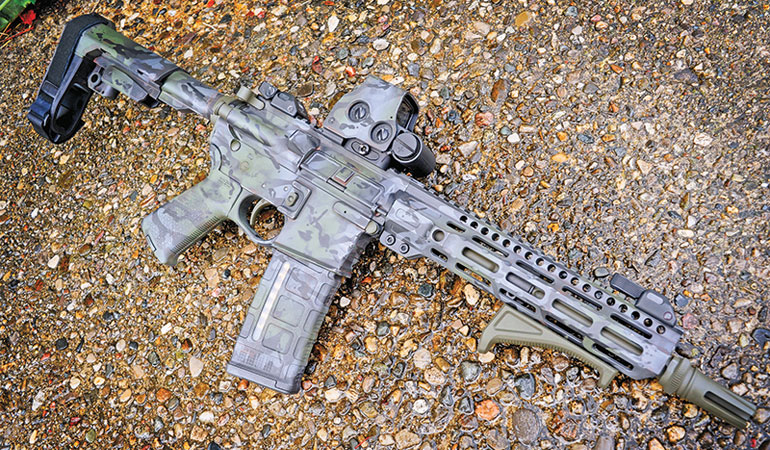
The Role of SSS Defence in India’s Defense Modernization
SSS Defence’s involvement in this project marks a significant step forward in India’s defense modernization efforts. As a trusted supplier in the Indian defense sector, the company brings expertise and innovation to the table, ensuring the highest standards for CERAKOTE application. This partnership not only strengthens ARDE’s capabilities in small arms but also has the potential to impact the broader defense industry, with future applications for larger systems.
The collaboration between DRDO’s ARDE and SSS Defence highlights the increasing role of indigenous defense companies in meeting India’s security needs, while also pushing forward ‘Make in India’ initiatives in advanced materials and technologies.